Conductive Printing
As the years passed, and faster now almost than we can follow, the bulky, energy and space- consuming wonders of yesterday have been replaced with lighter, smaller and more cost-effective, environmentally friendly alternatives. Massive, room-filling vacuum tube monstrosities we once called computers now fit in the palms of our hands. And Conductive Printing helped make it possible.
It’s not a new technology. Most sources agree that the screen printing process itself can be traced back to China’s Song Dynasty in 960-1279AD. Printed electronics have been with us in one form or another since the 1940s, though pine wood soot has been replaced by synthetic pigments, dyes, and metallic particles for improved conductivity and bond strength. Membrane switches only made their debut in the early 1980s.
Through experimentation, technological advancement and continual improvement– the latter an accepted tenet of most modern quality systems – Conductive Printing now incorporates an astounding range of field-proven standards; specialized inks, materials and streamlined manufacturing processes that enable a world of possibilities that our axe bearing ancestors could only have seen as magic.
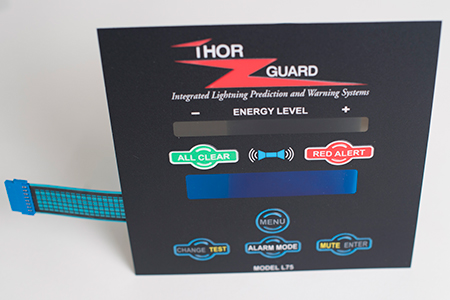
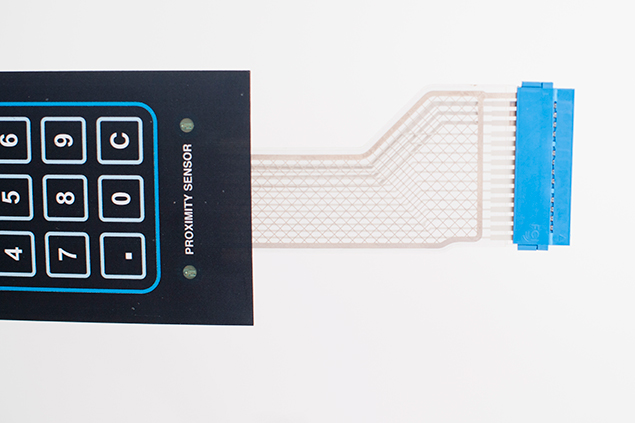
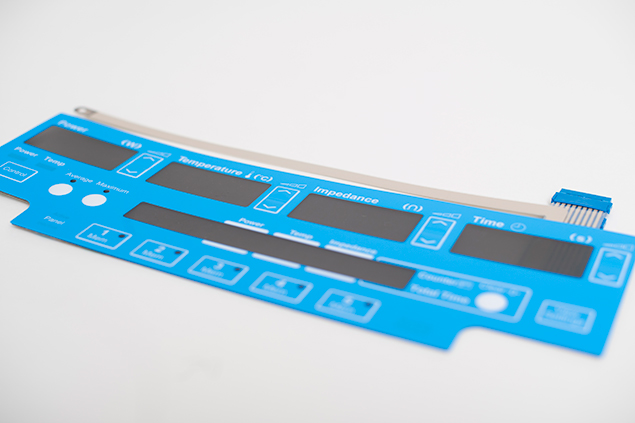
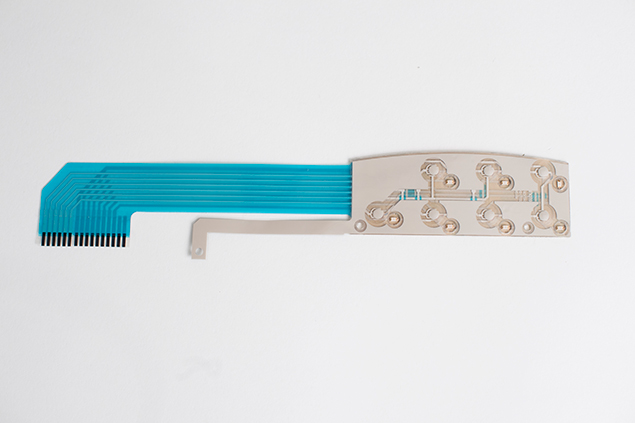
Our Capabilities
Screenprint/Dow has an impressive array of printing methods at their fingertips as you’ll see elsewhere on this site, but Screen Printing remains the time-honored method of choice for Conductive Printing. Along with select metallic conductors of low sintering temperatures, UV, solvent and water-based ink systems of varying viscosities, conductive epoxies, resistive and non-resistive carbon and graphite blends, clear encapsulates, UV curable dielectrics and more can all come into play to meet your specific requirements. Silver is the most common conductive ink, mainly because its oxide form also conducts.
Often print-treated and heat-stabilized, traditional Polymer Thick Film (PTF) substrates, both flexible and rigid are used for the printed base. Polyester resists tearing and humidity, is cheaper than polyimide, and forms better than polycarbonate.
Screenprint/Dow most often uses Conductive Printing for the trace circuitry of Membrane Switches, but we’ve yet to find its limits. Silver, Carbon, and printed dielectrics, using solid or interdigitated contact pads, multi-layered printing and more as directed by your supplied matrix can work in concert with the many types of switches you can discover here. Printed ESD, EMI/RFI, and ITO shielding can be incorporated, as well as flat cables, printed resistors, slide potentiometers, thru-hole vias, use of select surface mount components like LEDs, tactile Metal Domes as active or passive elements and more!
Dynamic environments and emerging fields such as smart packaging, NFC, VHF/UHF RFID tags and labels, touch screens, antennas, medical electrodes and bio-sensors and photovoltaics can all benefit from Conductive Printing’s advantages over older technologies, such as ease of manufacture, cosmetic appeal, design flexibility, slim, space-saving options and higher volumes at reasonable cost.
Let our application experts guide your projects to the best-suited solutions for you!